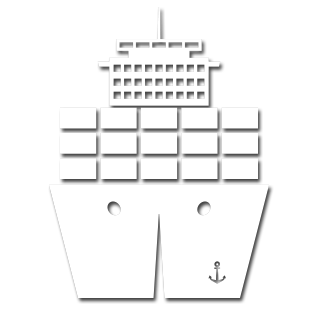
Calculations and Simulation
Marine Services
Calculations and Simulation
We use FEM analysis to solve simple and complex structural, static, dynamic, thermal problems … Customizing and adapting the solutions to the clients needs.
For the analysis and resolution of acoustic problems we use the SEA method (Statistical Energy Analysis). We also have specific software for naval acoustic analysis.
- Vibration, Noise and Underwater Radiated Noise Prediction Calculation
- Acustic Insulation Optimization
- Static, Dynamic and Thermal Analysis
- Torsional, Lateral and Axial Vibrations in Shaft Lines Calculation
- Stability Calculations
- Double Elastic Mounting Design and Calculation
- Steel and Composite Material Ship Structural Design
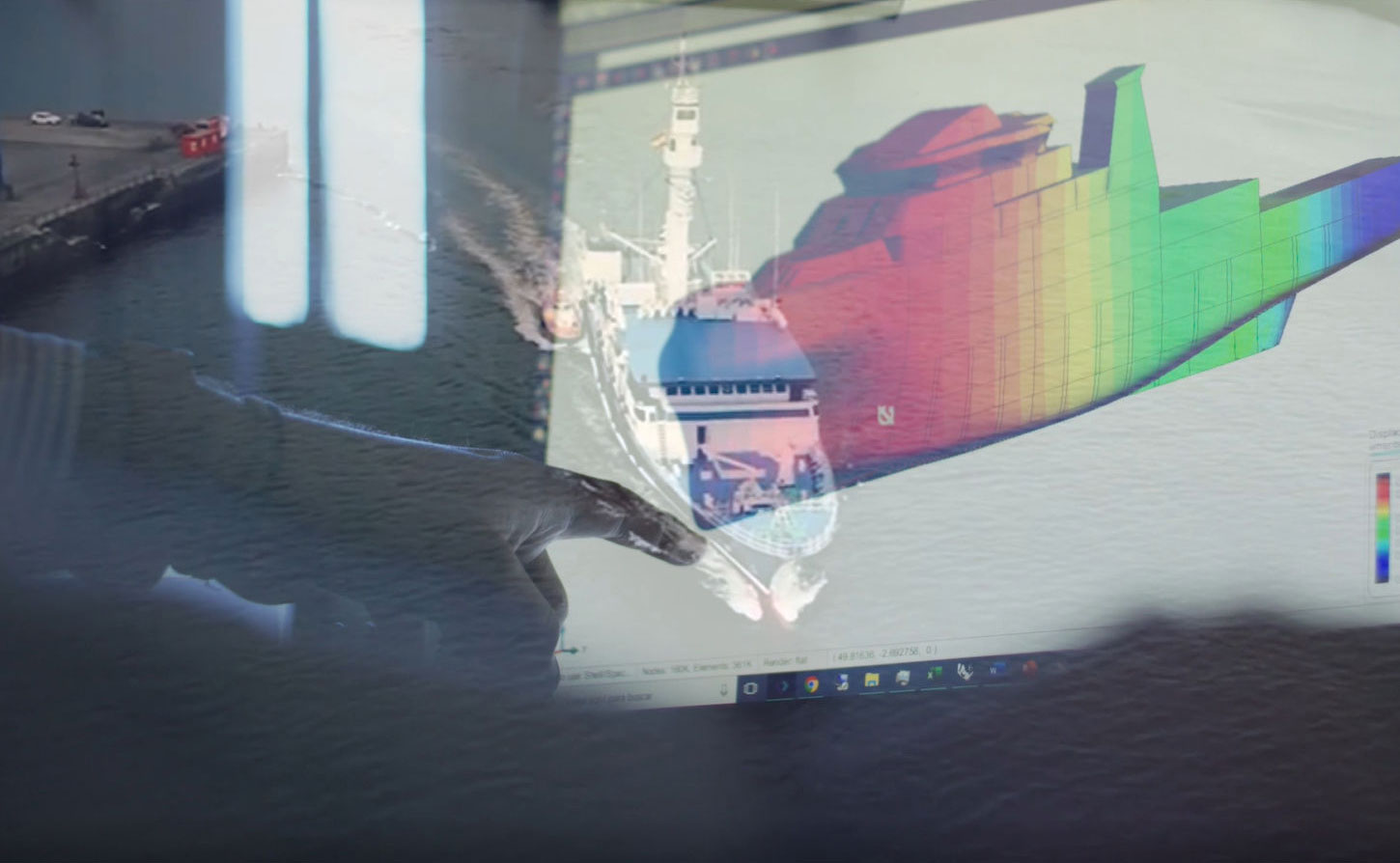
We are vibration and noise consultants with national and international recognition
We validate our calculation with measurements and tests!
VIBRATION PREDICTION CALCULATION
For this purpose TSI develops a three-dimensional (3D) Finite Element Mathematical Model of the whole ship structure. This model takes into account structural particularities, distributed masses, effects of entrained water and excitation forces.
The “expected vibration levels” throughout the vessel structure would be obtained by means of the corresponding Forced Response Analysis which consists on applying to the mathematical model those forces induced by the main vibration sources.
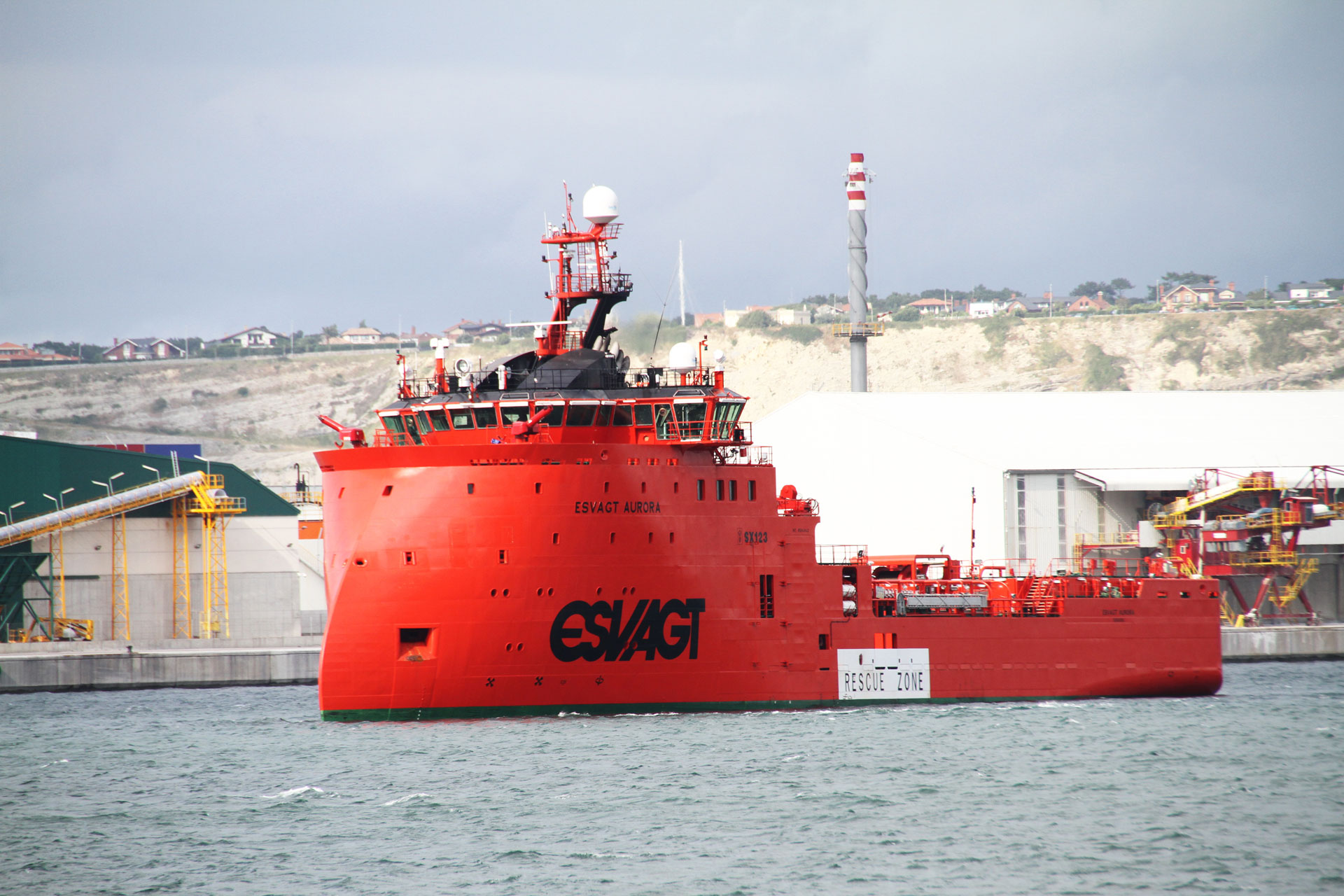
NOISE PREDICTION CALCULATION
In order to predict noise levels at work areas, Navigation Bridge, laboratories, Sonar Space and accommodation spaces, TSI develops a mathematical model by means of SEA Method (Statistical Energy Analysis)
and estimate the expected noise levels at each location of the vessel. Results obtained from the Noise Prediction are compared to those stated in the Specification. In those areas with noise levels exceeding the limits, corrective actions or complementary noise insulations are proposed and agreed with the Shipyard/Shipowner in order to reduce these levels. By means of this calculation, the expected noise levels are obtained at the different locations of the ship. An acoustic isolation optimized for compliance with the limits of the Specification is defined, avoiding overloads in the weight of the ship due to unnecessary isolation.
TSIdevelops a three-dimensional (3D) Finite Element Mathematical Modelof the whole ship structure
UNDERWATER RADIATED NOISE PREDICTION CALCULATION
The URN analysis of a vessel consists of studying the energy transfer from the noise source to the sea. TSI performs an URN analysis of the vessel, which consists in the combination of two (2) calculation/simulation models to study the noise generation in all the frequency range: FEA / BEM for the low frequency range (16 ~200 Hz) and SEA model for the high frequency range (250 – 10000 Hz). This calculation method has been validated through experimental results in order to obtain satisfactory results for the low and high frequency range.
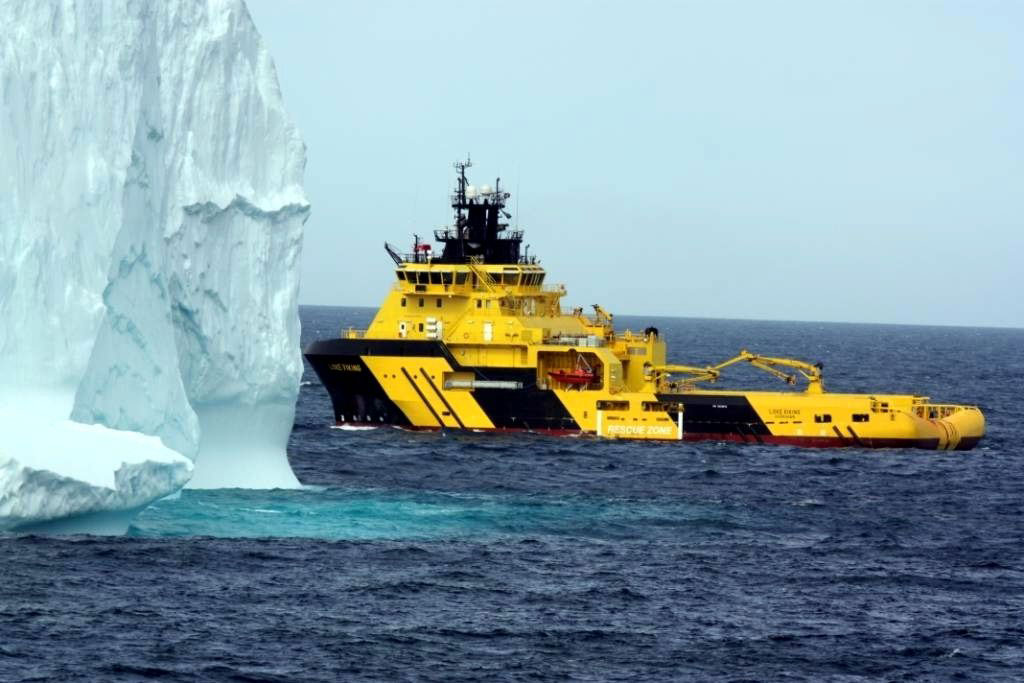
STATIC, DYNAMIC AND THERMAL ANALYSIS
Static analysis allows to study the structural strength and deformations of any geometry by simulating its behaviour under static loading. This type of analysis provides sufficient information to design any structure and optimize material use.
Dynamic analysis is used to study the behaviour of structures, elements or components subject to variable loading in the time or frequency domain.
- Modal Analysis: Definition of modes of vibration.
- Frequency response analysis: Estimation of vibration levels.
- Transient Dynamic analysis: Linear and non-linear, blast analysis, shock analysis.
- Response spectrum analysis, Random response: Seismic analysis. FEM analysis can also be used to evaluate other physical phenomena such as heat transfer. Thermal analysis allows to develop safer and more efficient products and processes.
CALCULATION AND SIMULATION I OTHER CALCULATIONS
• stability calculation.
• torsional, lateral and axial vibrations in shaft lines calculation.
• double elastic mounting design and calculation.
• shock analysis..
• modal analysis.
• steel and composite material ship structural design.
• correlation of test data with fem model and numerical simulation.
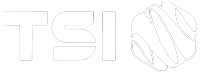